The operator tested and inspected casing used in drilling South Texas wells and found no damage that prevented casing reuse, with minor repairs.
Drilling with casing provided ConocoPhillips an effective means to reduce drilling costs in South Texas, with no observed reduction in the casing’s mechanical integrity. In addition to following traditional drilling practices – like minimizing dog legs – wear bands and stabilizers can be installed to mitigate effects of wear and fatigue when drilling with casing. Inspection of a string of 7-in. casing used to drill 6,232 ft, and successful completion of 82 intervals over the last three years provide convincing evidence that neither wear nor fatigue are significant factors for casing used for drilling.
INTRODUCTION AND BACKGROUND
ConocoPhillips adopted a drilling with casing program in July 2001 to reduce drilling costs in its South Texas
operations.1,2,3 While eliminating drill string tripping and reducing lost circulation and well control incidents has significantly increased drilling efficiency, use in drilling also subjects the casing to atypical wear and damage. The inability to accurately measure this damage has created a concern both within the industry and ConocoPhillips that using casing for drilling operations may compromise the mechanical integrity of the material.1,3 A reduction in mechanical integrity is a heightened concern throughout the life cycle of the wellbore since it can result in extensive well intervention, or well loss. When used for drilling, the casing
transmits torque and bit weight through rotation of the string and mechanical compression of the bottom portion of casing. These operating conditions generate two types of damage: 1) Wear: Side loads, or lateral loads, are applied to the casing due to wellbore curvature and buckling; and 2) Fatigue, which occurs when metal is subjected to cyclic loads that change the microstructure and promote crack development. This is generated by rotating the casing when it is bent and through buckling in the lower portion of the string.4 Fatigue cracks can occur in the tube body, pin ends or couplings, and act as stress concentrators. Increased stress levels from either wear or fatigue cracks reduce the casing’s capacity to withstand internal/external
pressure, and tensile loads. The operator recognized the potential risks associated with wear and fatigue. Stabilizers and wear rings are routinely used to mitigate this damage. Since the casing is not normally tripped, however, the string cannot be inspected for wear and fatigue. In South Texas, ConocoPhillips evaluated this concern through two approaches. First, while drilling a Zapata County Lobo well, it had to pull and lay down the 7-in. casing after drilling from 884 ft to 7,116 ft (6,232 ft). This allowed for inspecting thecasing and collecting first-order data regarding the wear/fatigue damage, but offered only a single data point. Additionally, the operator fracture stimulates its South Texas wells, which provides second-order data regarding damage to the string. Data from both approaches are presented here. ConocoPhillips has had a sustained multi-rig development program in the Lobo trend of South Texas since 1997. After optimizing the drilling program using conventional drilling methods, it conducted a field trial of the patented Casing Drilling system, followed by expansion to three Genesis rigs with 86 wells drilled to date using this technology.3 A typical casing and completion program for these wells is shown in Fig. 1. The system uses a wireline retrievable BHA and a casing string, as shown in Fig. 2. Recognizing the risks associated with abrasion, wear bands are crimped on the casing below couplings on a lower portion of the casing string, Fig. 3. Stabilizers,
are also crimped on the casing about every 1,000 ft to serve as keyseat wipers. Additionally, the stabilizers minimize deflection from buckling and reduce cyclic stress that drives fatigue.
INSPECTION RESULTS
While drilling a Zapata County Lobo well, a string of 7-in. 23-lb Mav95/P-110 BTC casing was used to drill 6,232 ft of 8⅞-in hole. While this occurrence resulted in non-productive time, it allowed inspection of the 7-in. casing for wear and fatigue cracks to provide firstorder data on the casing’s mechanical integrity. A total of 165 joints were sent to a storage yard for inspection. The pipe was cleaned and inspected as follows.
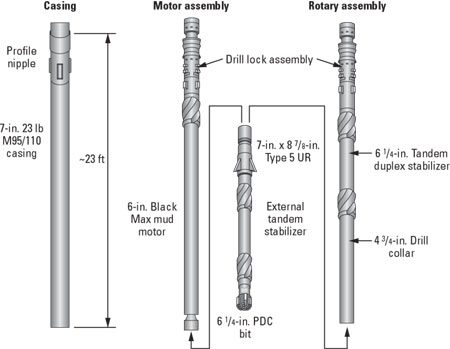
1. Tubes. Visual Tube Inspection. Initial visual inspection was performed to detect obvious mechanical damage, such as formation cuts or excessively deep slip cuts. Full Length Drift. Each joint was drifted full length using a drift mandrel to detect areas with reduced ID. The mandrel complied with API RP 5A5 Electromagnetic Inspection. An electromagnetic inspection was performed over the full length, excluding end areas. The unit was standardized using a test standard prepared from the pipe inspected with OD longitudinal and transverse notches meeting API Spec 5 CT. The unit was re-standardized as recommended in API RP 5A5. Gamma Ray Wall Thickness. The tubes, excluding end areas, were inspected for wear and reduced wall thickness using a chord-type gamma ray system. Single-wall thickness was measured, which would detect both uniform and eccentric wear.
2. Connections. Visual Connection Inspection. Coupling and pin threads were cleaned and visually inspected for thread form and damage, such as galling, tearing and wear. The connections were evaluated based on serviceability, rather than new connection requirements, since they were used. Blacklight Connection Inspection. Coupling and pin ends on the bottom 30 joints were inspected using this method to detect fatigue cracks. These joints were selected as they were buckled/rotated during drilling. Since the focus of was fatigue cracks generated while drilling, the inspection was performed in accordance with Standard DS-1.5
No joints were rejected for fatigue cracks or wear (wall thickness < 87.5% of nominal wall thickness per API Spec 5CT for new casing). The connections had varying amounts of galling and wear, which is expected with the connections being made up and broken out. Soft wheels and flapper wheels dressed the threads beyond the L7 area (Perfect Thread Length) as specified in API Spec 5B. Of the 165 joints, 117 were
successfully field repaired. Of the remaining 48, 20 required rethreading the coupling end, 18 required rethreading the pin end, and 10 required rethreading both coupling and pin. After the inspections were completed, the 48 joints noted above were repaired and the entire string was used to successfully drill
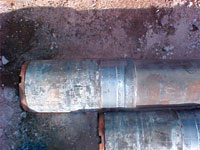
COMPLETION OPERATIONS
ConocoPhillips fracture stimulates all of its Lobo completions due to the low permeability and formation heterogeneity. High pressures and large volumes required in a fracture stimulation provide a second-order verification of casing mechanical integrity. That is, the casing is not directly inspected for reduced wall thickness and fatigue cracks, as was performed on string previously laid down, but rather pressure tests and pumping operations are performed, which demonstrate mechanical integrity. One can argue that successfully performing these completion operations does not quantitatively determine the degree of wear and fatigue; however, given that the operator has made over 82 completions with no failures due to wear or fatigue, indicating no wide-spread problem. When completing a Lobo well, a series of pressure tests are performed.
Before perforating, a frac stack is installed and the stack and production casing are pressure tested to 8,000 psi. The zone is then perforated and broken down. A typical zone requires 6,000 to 7,500 psi at 5 to 10 bpm, applied to the production casing, providing an additional pressure integrity test.
Before perforating, a frac stack is installed and the stack and production casing are pressure tested to 8,000 psi. The zone is then perforated and broken down. A typical zone requires 6,000 to 7,500 psi at 5 to 10 bpm, applied to the production casing, providing an additional pressure integrity test.
After break down, a data frac and frac are pumped down the production casing. In addition to internal pressure applied to the production string, the production casing by intermediate casing is pressured to 2,000 psi throughout the 1 to 3 hour pumping operation, thus pressure testing the intermediate casing above the top of cement. Again, no failures have occurred in the 82 completions made over the last 3 year period, which implies limited wear and fatigue damage to the casing.
ACKNOWLEDGEMENTS
The authors would like to thank ConocoPhillips for
its permission to publish this information, and Tesco
Corp. and GrantPrideco for the use of their graphics.
The authors would like to thank ConocoPhillips for
its permission to publish this information, and Tesco
Corp. and GrantPrideco for the use of their graphics.
By: T. Dhenny Farial Pratama, ST
Cementing Engineering
China Oilfield Service Ltd. (COSL)
thanks for nice sharing
BalasHapus